Im Batterie-Markt gibt es zahlreiche neue Entwicklungen. Das gilt auch für den Anwendungsbereich der Vakuumtechnik. Battery-News sprach mit Dr. Philipp Schurig, als Market Manager bei Pfeiffer Vacuum für die industrielle Lecksuche verantwortlich, über Anforderungen, Herausforderungen und Trends auf diesem Feld der Batterieproduktion.
Battery-News: Wie hat sich der Bereich der Batterieproduktion mit Blick auf Ihr Unternehmen in den vergangenen Jahren entwickelt?
Dr. Philipp Schurig: Seit unserem letzten Interview im Dezember 2020 hat sich in diesem Markt sehr viel getan. Die Anzahl der geplanten Gigafabriken in Europa ist weiter gestiegen. Die etablierten Zellhersteller und Anlagenlieferanten aus Asien spielen dabei eine große Rolle, da sie langjährige Erfahrung in der Realisierung solcher Großprojekte besitzen. Gleichzeitig gewinnt auch das Batterie-Recycling stetig an Bedeutung. Vor dem Hintergrund des zunehmenden Batteriezellenbedarfs werden hohe Ansprüche an die Produktivität der Gigafabriken gestellt – aber auch an einen schnellen Service, sollte es zu Ausfällen oder Stillständen kommen. Die hohe Qualität europäischer Anlagen- und Maschinenbau-Unternehmen und von deren regionalen Lieferketten und Service-Netzwerken ist ein großer Vorteil gegenüber den asiatischen Playern. Auf jeden Fall haben die steigenden europäischen und asiatischen Aktivitäten der Anlagenbauer im Batteriemarkt einen wachsenden Bedarf für Vakuumtechnik ausgelöst, den wir mit unserem Produktportfolio bedienen können.
Battery-News: Was sind derzeit die Treiber im Markt? Welche Trends und damit zusammenhängende Herausforderungen erkennen Sie aktuell?
Schurig: In diesem dynamischen Markt existieren unterschiedliche Triebkräfte, sowohl bei den Batteriechemien als auch bei der Produktionstechnik. Es etablieren sich stetig neue Chemie-Varianten – wie Lithium-Eisenphosphat-Batterien, Natrium- oder Schwefel-Verbindungen – und neue Typen wie Semi-Solid-State oder All-Solid-State auf Basis von Polymeren. Diese neuen Chemien bringen ihre eigenen Fragestellungen mit sich – zum Beispiel, welche Produktionstechnologien dafür verwendet werden und ob dafür bereits installierte Fertigungsstraßen genutzt werden können. Außerdem befinden sich die Batteriechemien und -typen in unterschiedlichen Entwicklungsreifegraden, von der Forschung bis hin zu Prototypen. Aus der Sicht des Anlagenbaus muss der CO2-Fußabdruck der gesamten Batterieproduktion deutlich gesenkt werden, um die politisch vereinbarten Ziele erreichen zu können. Die größten Hebel dafür bilden die Nutzung deutlich energieeffizienterer Produkte genauso wie neuartige Prozesse, die energieintensive Produktionsschritte komplett ersetzen können.
Es besteht Konsens darüber, dass der europäische Anlagenbau innovative Lösungen für existierende Prozesse finden muss, um den Abstand zum dominierenden asiatischen Markt zu verringern.
Dr. Philipp Schurig,
Pfeiffer Vacuum
Battery-News: Welche Erkenntnis haben Sie als Teilnehmer des „Future Battery Forum“ im vergangenen Jahr in Berlin gewonnen?
Schurig: Wir haben wahrgenommen, dass ein Konsens darüber besteht, dass der europäische Anlagenbau innovative Lösungen für existierende Prozesse finden muss, um den Abstand zum dominierenden asiatischen Markt zu verringern. Dabei werden für die europäischen Produzenten die Innovationskraft, das Wissen über europäische Regularien und die jahrzehntelange Erfahrung aus der konventionellen Automobilbranche essentiell sein. Unternehmen und Universitäten arbeiten bereits gemeinsam an neuartigen Technologien, mit denen sich etablierte Prozesse verbessern lassen – etwa beim Laser-Drying – oder sogar komplett ersetzt werden können – wie beim Dry-Coating. Derzeit bilden sich auch immer mehr Konsortien von Unternehmen, die mit ihren Kompetenzen die Realisierung schlüsselfertiger Lösungen und Teillösungen für die Batterieproduktion anbieten.
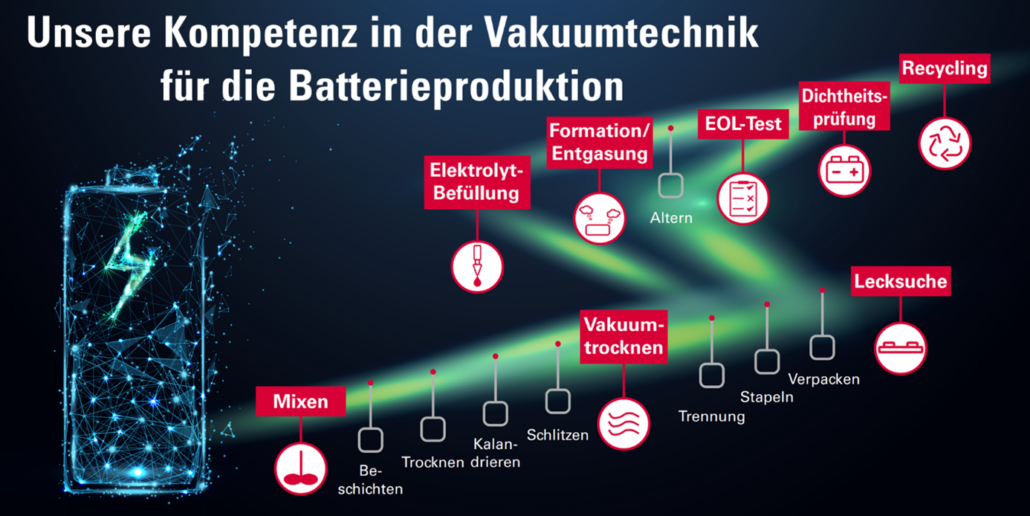
Battery-News: Während Europa sich immer mehr zu einem Markt für die Zellproduktion entwickelt, wächst auch der Recycling-Markt heran. Wo und mit welchen Lösungen hat Pfeiffer Vacuum sich im Lifecycle der Batteriezelle positioniert?
Schurig: Wir sind mit unseren Produkten in einigen Phasen dieses Lifecycles aktiv. Unsere Grafik zeigt hier nur die Schritte innerhalb einer Battery-Gigafabrik, in denen Vakuum benötigt wird. Allerdings werden Vakuum- oder Dichtheitsprüftechnologien schon in der Herstellung von Materialien für die Produktion genutzt, zum Beispiel in der Beschichtung der Ausgangs-Coils für den Arbeitsschritt „Beschichten“ oder in der vorgelagerten Dichtheitsprüfung der zylindrischen und prismatischen Batteriezellkomponenten.
Battery-News: Auf welche besonderen Innovationen blicken Sie gerne zurück?
Schurig: Eine unserer letzten Produktneuerungen sind die Wälzkolbenpumpen der Reihe „Okta ATEX“ mit einem Saugvermögen von 5.400 oder 8.100 Kubikmetern pro Stunde. Dank ihrer Konstruktion und Temperaturüberwachung liefern diese Pumpen eine hohe Explosionssicherheit. Das hohe Saugvermögen, das vor allem bei der Vakuumtrocknung und beim Recycling benötigt wird, ermöglicht außerdem einen effizienteren Produktionsprozess. Ein anderer interessanter Parameter kann die Zusammensetzung des extrahierten Gases sein. Unser Massenspektrometer GSD 350 – speziell in der Ausführung des ThermoStar – erlaubt es, unter Entnahme geringster Gasmengen von gerade mal einem Kubikzentimeter das Gas bis zu einer Auflösung von 300 u zu analysieren. Neben diesen neuen Produkten können wir auch individuelle Services für den Batteriemarkt anbieten, zum Beispiel unsere Lecksuche. Damit können Kunden frühzeitig und ohne eigenen CAPEX-Invest gemeinsam mit unseren Applikationsspezialisten die richtige Lösung für ihre Herausforderungen in der Dichtheitsprüfung finden.
Die Dichtheitsprüfung von Batterien ist ein wichtiges Qualitätsmerkmal für den Batteriemarkt, da deren Sicherheit und Lebensdauer sowohl für die Hersteller als auch für die Nutzer von höchster Bedeutung sind.
Dr. Philipp Schurig,
Pfeiffer Vacuum
Battery-News: Was darf ein Interessent unter diesen Dienstleistungen genau verstehen? Was bietet der Service Kunden aus dem Batteriemarkt?
Schurig: Unter unserem Lecksuche-Angebot verstehen wir Machbarkeits- und Zykluszeitstudien, Auftragsmessungen und Restgasanalysen. Die Dichtheitsprüfung von Batterien ist ein wichtiges Qualitätsmerkmal für den Batteriemarkt, da deren Sicherheit und Lebensdauer sowohl für die Hersteller als auch für die Nutzer von höchster Bedeutung sind. Die größte Herausforderung für neue Technologien ist meist die Bestimmung einer „funktionellen“ Dichtheitsanforderung oder das am besten geeignete Dichtheitsprüfverfahren. Für beide Problemstellungen kann eine Machbarkeitsstudie sinnvoll sein. Wie solch eine Analyse ablaufen kann, haben wir vor kurzem in einem Webinar gezeigt. Für die Lecksuche unterhalten wir Applikationslabore in den USA, in Deutschland und in China, die mit modernster Vakuum-, Mess- und Analysetechnik ausgestattet sind und die 15 Prüfverfahren nach DIN EN 1779/ISO 20485 abdecken. Die Mess- und Analysetechnik ist für alle industriell gängigen Technologien ausgelegt, also etwa für Dichtheitsprüfung mit Luft oder mit Prüfgasen und für die Quadrupol-Massenspektrometrie.
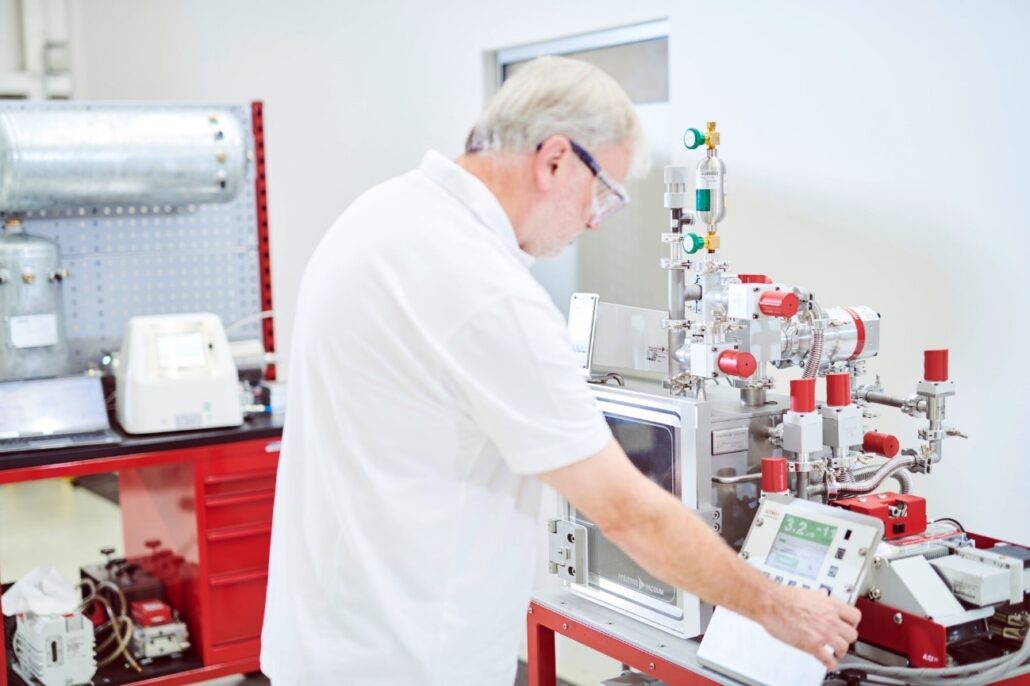
Battery-News: Weshalb ist die Dichtigkeit von Batterien so wichtig? Wie genau lässt sie sich in der Zellproduktion überprüfen und worin liegen dabei die Herausforderungen?
Schurig: Die Sicherheit und die Lebensdauer von Batterien werden mit Hilfe der Dichtheitsprüfung von der Zelle über die Batteriekühlung bis hin zum Batteriepack gewährleistet. Betrachtet man allein die Batteriezelle, kann die Dichtheit bis zum fertigen Produkt an mehreren Stellen überprüft werden: angefangen auf Komponenten-Ebene – zum Beispiel beim Deckel und beim Körper der Batterien –, direkt vor der Elektrolyt-Befüllung oder als „End of Line“-Prüfung. Eine große Herausforderung in der industriellen Dichtheitsprüfung von Batterien besteht in der Taktzeit, die aufgrund der notwendigen Wirtschaftlichkeit einer Gigafabrik äußerst schnell ist. Dadurch bedingt, sind meist entweder nur eine Stichprobenprüfung, eine Prüfung einzelner Batterien aus Produktions-Batches oder das Batch-Verfahren in Form einer gleichzeitigen Prüfung mehrerer Batteriezellen denkbar. Trotz des enormen Aufwands und der damit zusammenhängenden Kosten ist die Dichtheitsprüfung aus sicherheitsrelevanter Sicht unabdingbar. Das Eindringen von Feuchtigkeit in die Batterien kann dazu führen, dass sich, abhängig von der Batteriechemie, hochgradig toxische Gase oder Flüssigkeiten bilden oder andere Reaktionen in der Batterie ausgelöst werden, die die Integrität der Batterie stark gefährden.
Die Dichtheitsprüfung wird auch bei Feststoffbatterien eine bedeutende Rolle spielen. Nur, weil kein flüssiger Elektrolyt mehr vorhanden sein wird, bedeutet das nicht, dass die anderen Bestandteile innerhalb der Batterie nicht trotzdem stark mit Feuchtigkeit reagieren können.
Dr. Philipp Schurig,
Pfeiffer Vacuum
Battery-News: Bei Feststoffbatterien gibt es keinen Elektrolyten mehr in den Zellen, und auch die Kühlung ist in der aktuellen Form möglichweise nicht mehr notwendig. Wird eine Prüfung der Zellen auf Dichtheit dann überhaupt noch gebraucht oder denken Sie über Neuentwicklungen in diesem Bereich nach?
Schurig: Die Dichtheitsprüfung wird auch bei Feststoffbatterien eine bedeutende Rolle spielen. Nur, weil kein flüssiger Elektrolyt mehr vorhanden sein wird, bedeutet das nicht, dass die anderen Bestandteile innerhalb der Batterie nicht trotzdem stark mit Feuchtigkeit reagieren können. Ein bekanntes Beispiel dafür sind neuartige schwefelhaltige Batterie-Chemien, die bei Kontakt mit Feuchtigkeit Schwefelwasserstoff bilden können. Da sich die Forschung im Bereich der Feststoffbatterie in einem frühen Stadium befindet, lässt sich jetzt noch nicht abschätzen, wie die Dichtheitsprüfung in der industriellen Produktion genau vorgenommen wird. Wir können aber heute schon unterstützend zur Seite stehen – sei es eben mit Vakuumpumpen, die die ATEX-Richtlinien erfüllen, mit unserem Analyse-Equipment-Portfolio oder mit unserem Lecksuch-Service, der aussagekräftige Studien ermöglicht, ohne eine langfristige Investition in Ausrüstung tätigen zu müssen.