Der Preisdruck auf Batteriehersteller wird mit der zunehmenden Zahl der Anbieter immer größer. Leistungsfähige optische Prüfsysteme ermöglichen kurz- und langfristig ein großes Einsparpotenzial. Darüber sprachen die Battery-News mit Jochen Sander, der bei der Dr. Schenk Industriemesstechnik GmbH für das globale Batterie-Produktmanagement verantwortlich ist.
Battery-News: Welche Rolle spielen leistungsfähige kamerabasierte Prüfsysteme derzeit schon in der Batterieherstellung?
Jochen Sander: Solche optische Kontrollen werden immer wichtiger, um die Herausforderungen in der Batterieherstellung zu bewältigen – sowohl beim Ramp-up als auch in der laufenden Produktion. Früher wurden hochwertige Systeme oft als kostspielig wahrgenommen und einfache Systeme aus Asien verwendet. Wir beobachten gerade einen Wandel und stellen etliche Produktionen um.
Battery-News: Wie lassen sich dadurch Einsparungen in der Herstellung erzielen?
Sander: Meist spielen folgende Aspekte eine Rolle: weniger Produktionsausschuss durch genauere Einhaltung des Prozessfensters, weniger Support-Aufwand für die Kontrolle, Prozessverbesserung durch Nutzung von mehr und besseren Qualitätsdaten, höhere Qualitätsanforderungen vor allem aus der Autoindustrie und Platzeinsparung. So kann zum Beispiel eines unserer Systeme gleichzeitig drei Kontrollen vornehmen: die Defektprüfung der Oberfläche, eine Vermessung sowie die Kontrolle der Materialeigenschaften.
Battery-News: Können Sie ein konkretes Beispiel nennen?
Sander: Einer unserer Kunden hat vor Kurzem eine 45-prozentige Senkung des Produktionsausschusses im Elektroden-Coating erzielt – primär durch den Einsatz unserer Prüfsysteme. Diese Einsparung wurde möglich, da unsere Inspektion kleinere Fehler erkennt und sicherer einzelnen Defektklassen zuordnet. So konnte der Kunde das verfügbare Prozessfenster besser nutzen. Ganz nebenbei sank der Betreuungsaufwand für das Kamerasystem: Nach der Einrichtung musste der Qualitätsexperte in den ersten knapp zwei Wochen noch einige Fehlerbilder der KI zeigen, danach lief das System aber ohne weiteren Support-Aufwand – was er von seiner bisherigen Kontrolle nicht gewöhnt war, wie er sagte.
Battery-News: Wie gelingen Ihrem Unternehmen solch deutliche Verbesserungen?
Sander: Da könnte ich einiges ins Feld führen, konzentriere mich aber lediglich auf zwei Punkte, die bei Batterien besonders wichtig sind: Beleuchtung und künstliche Intelligenz. Mit unserer MIDA-Technologie wechseln wir bis zu 280.000-mal in der Sekunde zwischen Beleuchtungen aus unterschiedlichen Richtungen. Wir übertragen dazu das menschliche Vorgehen in die automatische Kontrolle, denn von Hand würde man den Prüfling auch jeweils in die beste Position drehen, um Fehler optimal zu erkennen. In der automatischen Prüfung übernehmen das die Beleuchtungen aus verschiedenen Richtungen. Da die Kanäle auch miteinander verrechnet werden, haben wir bei drei bis vier Beleuchtungen sechs- bis elfmal mehr Bildinformationen. Das macht die genannten Verbesserungen erst möglich.
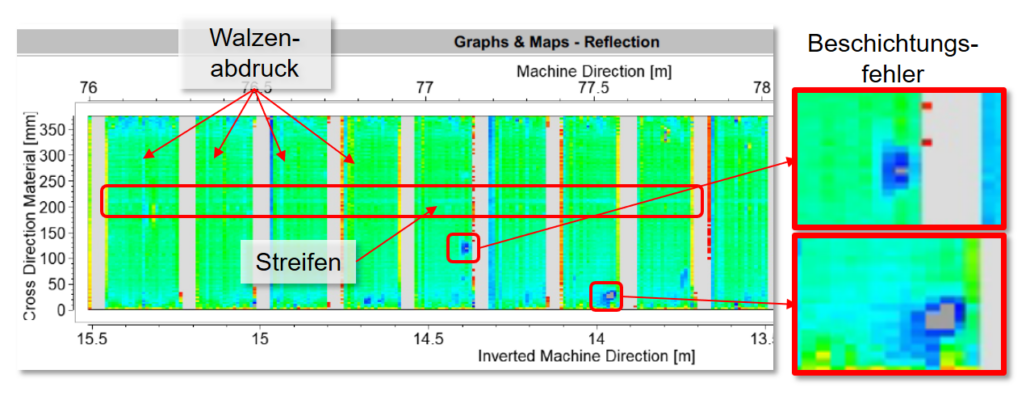
Battery-News: Welche Rolle spielt künstliche Intelligenz genau in diesem Kontext?
Sander: Statt einer „allwissenden“ KI, die aufwendig zu trainieren und komplex in der Handhabung ist, setzen wir auf einen Multi-Step-Ansatz. Dadurch, dass die KI für spezifische Auswertungen optimiert ist, erreichen wir die höchste Leistung. So filtern wir in den Kameras mit KI einen Datenstrom von 140 Gigabit pro Sekunde in Echtzeit. Das entspricht ungefähr dem 28.000-Fachen eines HD-Videostreams. Auf dem PC werden danach nur noch die kritischen Fehler gezielt ausgewertet. Durch diese massive Rechenleistung können komplexere Verfahren verwendet und mehr Fehler erkannt werden. Außerdem sind diese Systeme schneller als herkömmliche. Auch Bahnbreiten von mehr als zehn Metern oder Slitting-Geschwindigkeiten von 800 Metern pro Minute sind so leicht umsetzbar.
Battery-News: Sind solche leistungsfähigen Systeme nicht aufwendig in der Einrichtung und intensiv im Support?
Sander: Umständliche Bedienung findet man in jeder Preisklasse. Unser Ansatz ist immer, dass der Kunde von der dahinterstehenden Komplexität nichts merkt. Dahinter stecken die Erfahrung aus fast 40 Jahren Entwicklung und das Wissen aus unterschiedlichen Branchen wie Glas, Metall und Papier. Der durchschnittliche Implementierungsaufwand liegt für neue Systeme bei rund zwei Wochen – jeweils zur Hälfte beim Anlagenbediener und beim Qualitätsverantwortlichen.
Battery-News: Sie erwähnten anfangs die Möglichkeit, mit einem System drei unterschiedliche Kontrollen vorzunehmen. Können Sie da ins Detail gehen?
Sander: Unsere Systeme vollbringen drei Dinge gleichzeitig: das Auffinden von Fehlstellen in der Oberfläche – also etwa Partikel, Kratzer, Risse, Löcher oder Walzenabdrücke; dann eine hochgenaue Vermessung, zum Beispiel mit Blick auf den Versatz verschiedener Coating-Layer; und die Überprüfung der Materialeigenschaften, beispielsweise die Homogenität, Rauheit und so weiter. Die damit verbundene Platzeinsparung senkt den CapEx.
Battery-News: Fehlstellen und Vermessung dürften allgemein bekannt sein. Was genau aber meinen Sie mit „Materialeigenschaften“?
Sander: Die Kontrolle von Materialeigenschaften hat sich bei der Früherkennung aller Arten von Materialabweichungen bewährt. Bei Separatorfolien können wir Änderungen in der Beschichtungsstärke im Sub-Mikrometer-Bereich bei voller Produktionsgeschwindigkeit und über die ganze Folienbreite hinweg von bis zu zehn Metern erkennen. Bei Elektroden sind das sämtliche Coating-Schwankungen oder Walzenabdrücke. Für diese Kontrolle nutzen wir Informationen der unterschiedlichen Beleuchtungskanäle. Ändern sich die Materialeigenschaften, ändern sich auch die optischen Eigenschaften, zum Beispiel Reflexion, Transmission, Glanz oder Streuung. Unsere Systeme werten das aus und können auf diese Weise selbst minimale Änderungen erkennen.
Battery-News: Was sind Ihrer Meinung nach die entscheidenden Faktoren für eine erfolgreiche Qualitäts- und Prozesskontrolle in der Batteriezellproduktion?
Sander: Die Batteriezellfertigung gehört zu den dynamischsten Produktionsbereichen weltweit. Häufige Fertigungsänderungen, der ständige Produktions- und Verbesserungsdruck und die knappen Personalkapazitäten sind nur einige Merkmale. Das erfordert von den Prüfsystemen eine hohe Flexibilität, damit sie mit den Anforderungen des Kunden wachsen können. Der möglichst einfache Zugang zu den erfassten Daten und ein kompetenter, lokaler Support sind genauso wichtig wie leistungsfähige Technologien. Bei Dr. Schenk teilen wir unser Wissen mit den Kunden, um maßgeschneiderte Lösungen zu entwickeln.