Die 12. Elektromobilproduktionstage (EPT) in Aachen haben Branchenführer, Innovatoren und Forschende zusammengebracht, um Fortschritte in der Fertigung von Komponenten der Elektromobilität zu ergründen. Die vom Lehrstuhl PEM der RWTH Aachen und der Fraunhofer FFB organisierte und von Battery-News als Medienpartner unterstützte Veranstaltung hat sich zu einer wichtigen Plattform für Diskussionen über die Zukunft der Produktion von Elektrofahrzeugen entwickelt. Der Fokus der diesjährigen Veranstaltung lag auf Effizienzsteigerung, Innovation und der Skalierung neuer Technologien für die Massenproduktion.
Bedarf an flexibleren Produktionslinien
Zahlreiche Experten unterschiedlicher Herkunft betonten dabei die Notwendigkeit einer engen Zusammenarbeit von Forschungseinrichtungen und Industrie, um die Wettbewerbsfähigkeit im globalen Markt zu sichern. In Workshops und Diskussionen wurden die Herausforderungen bei der Skalierung von Produktionsprozessen für Elektromotoren, Batteriesysteme und Komponenten hervorgehoben und der dringende Bedarf an flexibleren, effizienteren Produktionslinien betont.
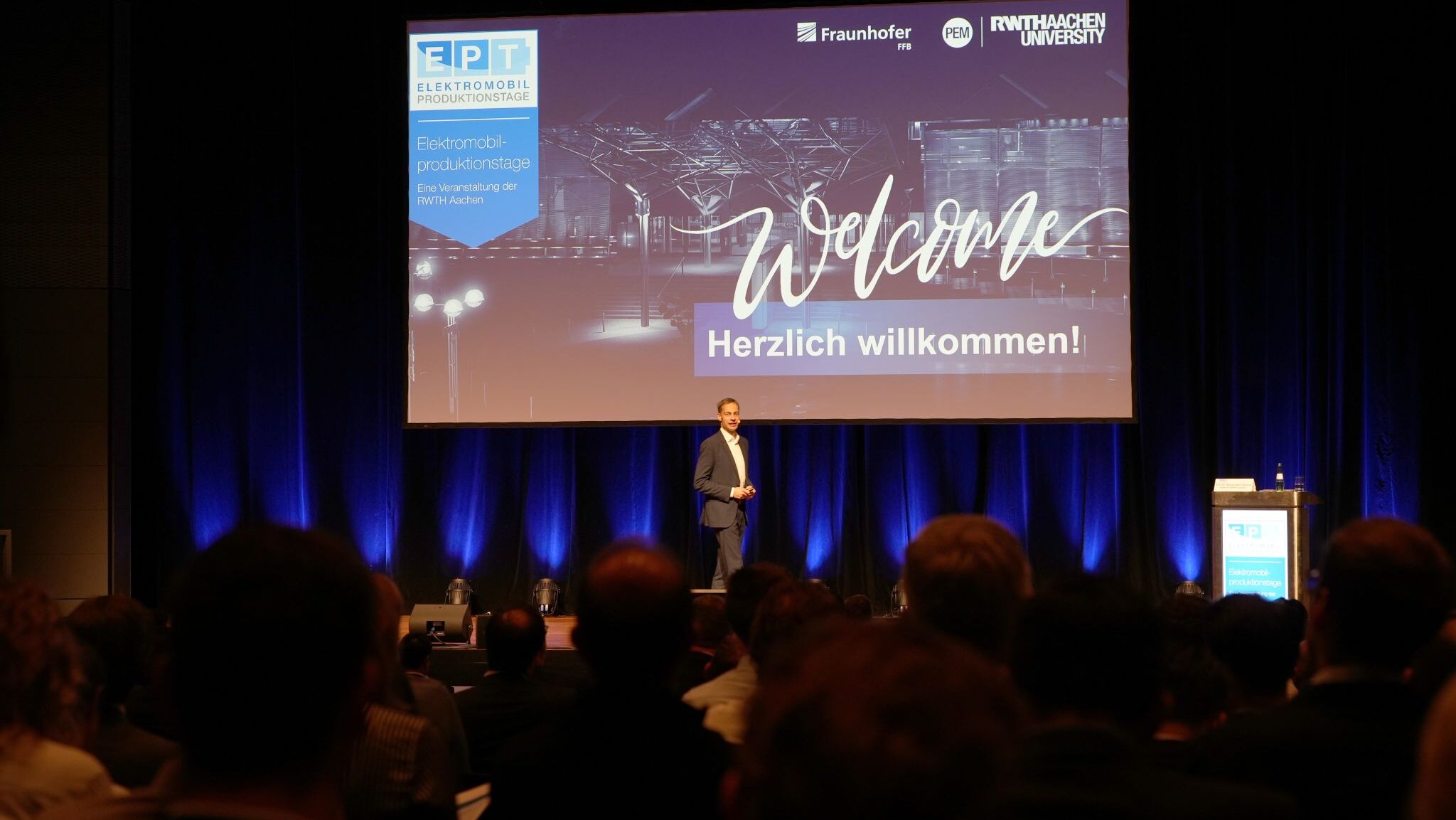
Von der Forschung in die Massenfertigung
PEM-Leiter Professor Achim Kampker betonte, dass eine Verbesserung der Effizienz bei der Herstellung sämtlicher Elektrofahrzeugkomponenten nicht nur die Kosten senken, sondern auch die weltweite Einführung von Elektrofahrzeugen beschleunigen würde. Die Fraunhofer-Forschungseinrichtung Batterizelle FFB gewährte Einblicke in ihre Funktion bei der Skalierung von Innovationen aus der Forschung bis zur industriellen Produktion und zeigte, wie sie dazu beiträgt, die Lücke zwischen Experimenten im Labormaßstab und der Anwendung in der Praxis zu schließen. Die FFB gilt als Beispiel dafür, dass die Produktion in Deutschland sowohl hinsichtlich der Kosten als auch mit Blick auf die Qualität im globalen Maßstab wettbewerbsfähig ist.
Drei „E-Mobility Production Awards“ verliehen
Am ersten EPT-Abend wurden zum zweiten Mal die „E-Mobility Production Awards“ vergeben, mit denen Akteure für ihre Beiträge zur Förderung der Herstellung von Komponenten der Elektromobilität ausgezeichnet werden. In diesem Jahr würdigte die Jury Leistungen in den beiden Schlüsselkategorien „beste E-Motor-Produktion“ und „beste Batteriesystemproduktion“. Das Publikum wählte unterdessen einen dritten Preisträger für die beste „Prozessinnovation in der Produktion von Batteriezellen und -systemen“.
- Der Preis für die beste E-Motoren-Produktion ging an die BMW Group für ihr Werk in Dingolfing. Die Jury hob die Fähigkeit des Werks hervor, eine breite Palette von Elektromotoren effizient zu produzieren und dabei das höchste Produktionsvolumen pro Quadratmeter unter allen Kandidaten zu erreichen. Das BMW-Werk zeichne sich durch den Einsatz selbst entwickelter Technologien und innovativer Produktionsprozesse aus, die durch einen hohen Automatisierungsgrad und strategische Patente vorangetrieben werden.
- Den Award für die beste Batteriesystemproduktion erhielt die „Volkswagen Group Components“ in Braunschweig. Die Jury lobte die Fähigkeit von Volkswagen, seine Batterieproduktion trotz erheblichen Kostendrucks und eines komplexen Produktionsumfelds schnell zu steigern. Der innovative Ansatz von VW bei der Integration von Produktionskapazitäten und der Umschulung von Mitarbeitenden ermöglichte es dem Unternehmen, diese Herausforderungen zu meistern und Batteriesysteme von höchster Qualität für eine breite Palette von Fahrzeugmodellen zu liefern.
- Der dritte Preis für die beste Prozessinnovation wurde vom EPT-Publikum in einer Live-Abstimmung ermittelt und wurde dem schwedischen Unternehmen Excillum für seine MetalJet-Technologie verliehen. Dabei handelt es sich um die hellste Mikrofokus-Röntgenquelle der Welt, die ein präziseres und schnelleres Scannen von Batteriematerialien ermögliche, was für die Qualitätskontrolle in der Batterieproduktion entscheidend ist. Die Innovation berge das Potenzial, die Produktionseffizienz erheblich zu steigern und höhere Qualitätsstandards im Herstellungsprozess zu gewährleisten.
Skalierbarkeit und Kosteneffizienz werden essenziell
Den Elektromobilproduktionstagen zufolge liegt die Zukunft in der Skalierbarkeit, Flexibilität und Kosteneffizienz. Ziel der 12. EPT war es zu verdeutlichen, dass es bei Innovationen in der Produktion von Elektromobilität nicht allein darum gehen darf, die aktuelle Nachfrage zu bedienen, sondern auch darum, sich auf die Zukunft vorzubereiten. Mit verstärkter Zusammenarbeit, größerer Flexibilität in der Fertigung und kontinuierlichen Fortschritten bei den Produktionsprozessen sei die Branche gut aufgestellt, um den weltweiten Übergang zur Elektromobilität voranzutreiben.