Beides gilt inzwischen als europäischer „Common Sense“: Für die Energie- und Verkehrswende muss sich die Automobilwirtschaft transformieren, und Europa muss dabei für eigene Kompetenzen und Kapazitäten vor allem im Bereich der Batteriezellfertigung sorgen. Mit Unterstützung der Politik wird derzeit stark in den Aufbau einer entsprechenden Produktion investiert. Doch wie kann sich die europäische Wirtschaft marktgerecht aufstellen?
Mehr als 135 Milliarden Dollar bis 2027
Die Marktforscher von Markets and Markets erwarten für die kommenden fünf Jahre einen Anstieg der weltweiten Nachfrage im Bereich der Lithium-Batterien für Elektrofahrzeuge von jährlich 19 Prozent. Dementsprechend wachse der Umsatz von 56,4 Milliarden US-Dollar aus dem Jahr 2022 auf 134,6 Milliarden US-Dollar bis 2027 mit einem Kapazitätsschwerpunkt von 50 bis 110 Kilowattstunden.
CATL unangefochtener Weltmarktführer
Die führenden Anbieter kommen bislang aus China, Südkorea und Japan. CATL deckte im ersten Halbjahr 2023 mehr als ein Drittel des Weltmarktes für Elektrofahrzeug-Akkus ab, während BYD mit knapp 16 Prozent auf den zweiten Platz vorrückte – direkt dahinter LG Energy Solution mit 14,5 Prozent. Auf den weiteren Rängen folgen – mit einstelligen Prozentwerten – Batterie-Schwergewichte wie Panasonic, SK On, CALB und Samsung SDI. Allein die Top-5-Hersteller beanspruchen mehr als drei Viertel des Weltmarktes für sich. Häufig werden ihre Fertigungsstätten von großen Projektentwicklern als schlüsselfertige Lösungen errichtet.
Produktionsanlagen flexibel gestalten
Als relevanter Aspekt gilt die hohe Entwicklungsgeschwindigkeit der Batteriezellentechnologie. Derzeit sind Lithium-Ionen-Batterien in Form von Pouch-Zellen, Rundzellen oder prismatischen Zellen üblich, doch schon bald könnten neue Formate, Dimensionen oder Materialien relevant werden, zum Beispiel „All/Almost Solid State Batteries“ (ASSB). Um eine Produktionsanlage zukunftsfähig zu machen, muss sie flexibel anpassbar sein. Eine Digitalisierung auf dem Stand der Technik ist für eine solche Flexibilität unerlässlich – etwa in Form von digitalen Zwillingen. Ein digitales Abbild der Anlage ermöglicht eine einfachere Anpassung der Produktion, da schon in der frühen Planungsphase die Einflüsse eines neuen Produkts auf die Anlage virtuell getestet werden können – und die physische Umsetzung erst erfolgt, wenn in der Simulation sämtliche Probleme gelöst sind. Diese lässt sich später auch bei der Inbetriebnahme sowie bei der Wartung und Instandhaltung nutzen. Das setzt jedoch auch entsprechende Fähigkeiten in der digitalen Transformation voraus. Insbesondere Start-up-Unternehmen benötigen an dieser Stelle hier häufig Unterstützung.
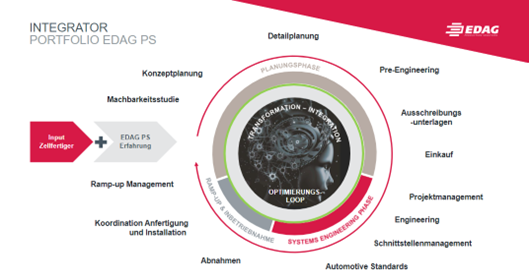
Hinzu kommt der Aspekt der Nachhaltigkeit in der Produktion. In naher Zukunft werden zahlreiche Fahrzeugbatterien zur Wiederverwendung und Nachnutzung anfallen. Die EU hat bereits Regelungen zur Verwendungsquote von Recycling-Stoffen, aber auch in Bezug auf den CO₂-Fußabdruck der Produktion erlassen. Diese und eventuell folgende weitere Verschärfungen müssen beim Aufbau einer neuen Produktion bereits mitbedacht werden. Die Wettbewerbsfähigkeit europäischer Fertigungslösungen im Vergleich zu denen von asiatischen Anbietern mit niedrigeren Investitionen entscheidet sich auch anhand der Betriebskosten. Bessere OpEx-Werte, beispielsweise aufgrund einer deutlich niedrigeren Ausschussquote oder eines höheren Durchsatzes, können die Gesamtkosten („Total Cost of Ownership“, TCO) reduzieren – trotz der in Europa höheren Rohstoff- und Energiekosten.
Turn-key-Anbieter im Vorteil?
Sogenannte Turn-key-Anbieter können auf umfangreiche Erfahrungen setzen. Sie bieten als Projektentwickler alle nötigen Kompetenzen unter einem Dach, so dass wenig Koordinierungsaufwand entsteht. Dabei greifen sie auf bewährte Technik zurück und bieten an, Klone vergleichbarer asiatischer Produktionsanlagen auch in Europa zu erstellen – in vergleichsweiser kurzer Zeit. In Europa gibt es keine Anbieter vergleichbarer Größe, die alles aus einer Hand anbieten könnten. Alternativen lassen sich allenfalls über einen Integrator-Ansatz darstellen. Zum physischen Aufbau und Start der industriellen Fertigung sind unterschiedliche Kompetenzen gefragt, die sowohl die Projektentwicklung als auch branchenspezifische Besonderheiten und Elemente der Verfahrenstechnik umfassen und die in einem entsprechenden Konsortium zusammengeführt werden müssen. Zu den wesentlichen Schritten eines solchen Projekts gehören:
- Einrichtung eines zentralen Projektmanagements, das federführend die Teilnehmenden des Konsortiums und die verschiedenen Aufgaben koordiniert
- Machbarkeitsstudie, Konzeptplanung, Detailplanung und Spezifizierung des Equipments bis hin zur „Übersetzung“ in entsprechende Ausschreibungen
- Konstruktion der Anlagen
- Begleitung des Equipment-Aufbaus in der Produktionshalle
- Inbetriebnahme
- Anlagenhochlauf mit Maßnahmen zur Fehlerbehebung und Optimierung
Diese Aspekte miteinander zu verknüpfen, ist zeit- und kostenaufwendig, denn bislang handelt es sich dabei meist um individuelle Lösungen. Das kann sich indes negativ auf die Wettbewerbsfähigkeit auswirken, denn die Investitionskosten (CapEx) liegen höher als bei einer schlüsselfertigen Lösung. Zumindest aus dieser Perspektive sind asiatische Anbieter im Vorteil.
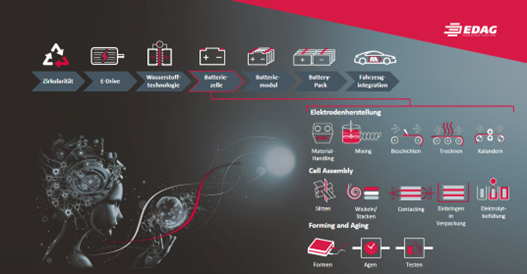
Gesamtkosten sind entscheidend
Tatsächlich zeigen schlüsselfertige Lösungen aber immer wieder Schwächen, die einem effizienten Betrieb entgegenstehen. Probleme beim Durchsatz und hohe Ausschussquoten machen den Betreibern zu schaffen. Auch gestalten sich Fragen zur CE-Kennzeichnung und zu anderen europäischen Normen – beispielsweise zum Arbeitsschutz – für Projektentwickler mit Sitz außerhalb der EU als enorme Herausforderung, die sich für die Auftraggeber nicht immer befriedigend lösen lassen. Diese müssen dann aufwendig nacharbeiten, was sowohl den Zeitvorteil aufzehrt als auch die Anfangsinvestitionen nach oben treibt.
Europäische Zusammenschlüsse
Ein Zusammenschluss von europäischen Spezialisten – sei es als Konsortium, als Joint Venture oder als ein vergleichbares Konstrukt – bietet daher Chancen, im scheinbar aussichtslosen Wettbewerb mit den Branchengrößen mit Hilfe wirtschaftlich attraktiver Lösungen zu bestehen. Um wettbewerbsfähig zu sein, benötigt die europäische Industrie Anlagen, die leistungsfähig und hocheffizient sind, moderne Zellen produzieren und sich flexibel an die dynamische technische Entwicklung in diesem Bereich anpassen lassen. Entsprechende Anbieter, die in ihrem jeweiligen Fachgebiet Spezialwissen und zukunftsfähige Lösungen mitbringen, gibt es zur Genüge. Einen Überblick zu relevanten Herstellern auf sämtlichen Stufen der Wertschöpfungskette bietet beispielsweise der „Battery Atlas“.
Produktions-Engineering, Simulation und mehr
Die Frage ist, wer einen solchen Zusammenschluss koordinieren und managen kann. Hier ist zum einen generelles Produktions-Know-how gefragt, aber auch spezifisches Wissen zu den Besonderheiten der Batteriefertigung. „EDAG Production Solutions“ kann diese Aufgabe übernehmen und darüber hinaus in verschiedenen Bereichen selbst tätig werden. Das Unternehmen bietet ein 360-Grad-Produktions-Engineering, wozu auch die Anlagenplanung und -optimierung zählt, sowie die Digitalisierung von Abläufen und Erfahrungen in der Simulation und der virtuellen Inbetriebnahme. Darüber hinaus engagiert sich die EDAG Group in mehreren Gremien und Konsortien für die Batteriezellenproduktion – darunter „FestBatt“ und „ProZell“ – und kann so auch in diesem Bereich auf Domänenwissen zurückgreifen. Hinzu kommen umfangreiche Branchenkontakte zu Unternehmen auf allen Stufen der Wertschöpfungskette.