In the race for the future of electric mobility, Tesla and BYD are pursuing fundamentally different battery concepts. While Tesla relies on 4680 cylindrical cells to maximize energy density and performance, BYD is taking a cost-efficient and safety-oriented approach with its prismatic Blade battery. A new teardown analysis conducted by researchers from Fraunhofer IKTS, MEET at University of Münster, and PEM of RWTH Aachen University, which was published in the Cell Reports Physical Science journal, provides detailed insights into the key technical differences between these two battery types and their implications for the electric vehicle industry.
Entirely different cell formats
According to the study, the core distinction lies in the cell format. Tesla’s cylindrical 4680 cell uses nickel-manganese-cobalt (NMC811) chemistry, achieving 241 watt-hours per kilogram of gravimetric energy density and 643 watt-hours per liter of volumetric energy density. This design enables longer driving ranges but also comes with challenges in thermal management. The study found that the Tesla 4680 generates 2.3 times more heat per volume than the BYD Blade cell under a 1C load, requiring advanced cooling solutions.
BYD battery attractive for mass-market cars
In contrast, BYD’s Blade battery, based on lithium iron phosphate (LFP) chemistry, prioritizes safety, longevity, and cost-effectiveness. Although its 160 watt-hours per kilogram of gravimetric and 355 watt-hours per liter of volumetric energy density is lower than Tesla’s, the Blade battery’s prismatic format enables better heat dissipation, reducing the need for complex cooling systems. This makes it an attractive choice for mass-market electric cars, where affordability and reliability are key selling points.
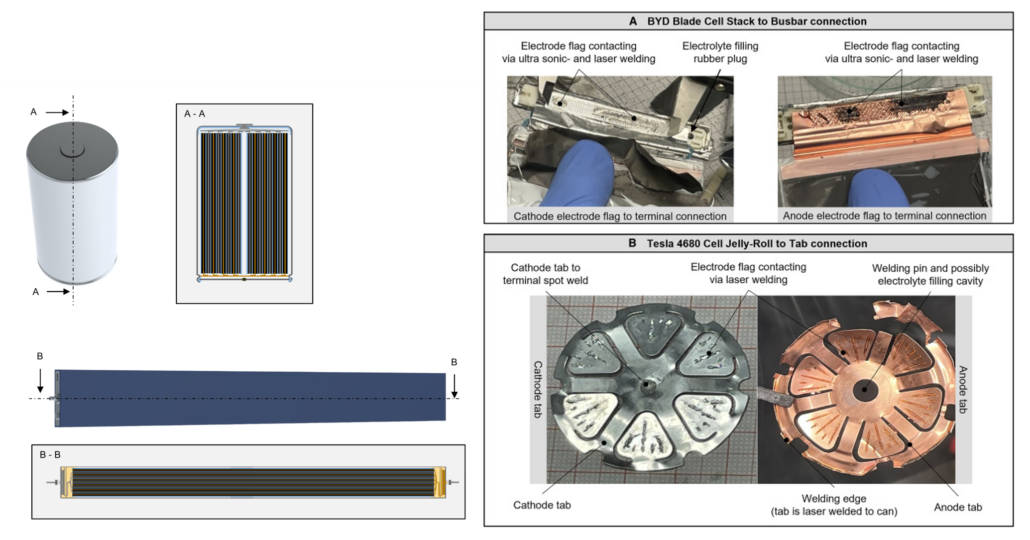
Manufacturing approaches also differ
Beyond chemistry and energy density, manufacturing approaches also reveal stark differences. Tesla employs a tabless electrode design, which improves electrical flow and minimizes resistance. The 4680 cell uses laser welding for electrode connections and a continuous coating process, enhancing efficiency in production. BYD, on the other hand, relies on a unique lamination process that ensures precise electrode stacking, allowing to create very large electrode stacks. The company also uses a combination of laser and ultrasonic welding, an innovative contacting strategy that allows for efficient space usage of the electrode to terminal contacts. Another crucial factor is cost: According to the authors, BYD’s Blade battery is approximately ten euros per kilowatt-hour cheaper in material costs than Tesla’s 4680 cell, making it an attractive option for manufacturers looking to reduce vehicle costs.
Tesla’s technology remains a benchmark
While Tesla’s 4680 battery is designed for high-performance, long-range electric vehicles, BYD’s Blade battery is engineered for cost efficiency, safety, and scalability, the study claims. With BYD recently overtaking Tesla in global electric vehicle sales, the company’s battery-first approach and aggressive cost advantages could have a lasting impact on the industry. However, Tesla’s 4680 technology remains a benchmark for high-performance electric cars, setting new standards in energy density and efficiency. As both manufacturers continue refining their battery technologies, studies like this teardown provide a critical reference point for the next generation of lithium-ion cell development.