The battery industry is on the move – and itʼs not always in a forward direction. In an exclusive interview with Battery-News, Dr. Alexander Timmer, Partner & Managing Director at Berylls by AlixPartners, discusses the current state of cell production in Germany and Europe, the challenges hindering the establishment of a circular economy, and the trends shaping the battery sector.
Battery-News: What recent developments in the battery industry have surprised you the most?
Dr. Alexander Timmer: The recent decisions either to continue investing in Germany or to cease further investments. Take SVOLT, for example – a company that has decided to halt its operations in Germany and stop investing in its facilities there. On the other hand, we see the positive commitment from Northvolt to move forward with its project in Heide, despite significant challenges faced by its Swedish parent company. Investing in Germany, establishing production expertise, and consolidating capabilities is no longer a given, as we now face conditions that are not conducive to industrial settlement.
“There will be significant market consolidation. The manufacturer landscape will thin out considerably.”
Battery-News: What market trends do you see for battery production in Europe, and how should companies respond to increasing competition?
Timmer: We are seeing a growing presence of Chinese players in the market – thatʼs no secret. However, what is less known or not fully assessed is that alongside a few major players, there is an overproportional number of mid-sized cell suppliers, leading to overcapacity. Depending on the region, these plants operate at 40, 50, or 60 percent utilization. Battery production, however, is a scale business that thrives on high utilization and low scrap rates. I anticipate significant market consolidation, with the first clear signs by 2025. The manufacturer landscape will thin out considerably.
Battery-News: What leads you to this assumption?
Timmer: We’re seeing the profit margins of cell manufacturers coming under pressure – a trend that has been apparent for some time. Therefore, major battery players must strategically ensure their investments in factories and production capacities remain as flexible as possible. Only with such flexibility can they adapt to short-term to medium-term fluctuations in production volume, which also provides greater financial breathing room. This challenge is underscored by the fact that every gigawatt-hour of production capacity typically requires an investment of about 100 million euros, while many cell manufacturers are operating with very slim single-digit profit margins. Investments in new plants in Europe are essential, even though we are already dealing with overcapacity. These are necessary to ensure “local content” and meet EU regulations. Thus, production localization in Europe must happen, even if importing products from China would be cheaper. Effective cash flow management will be key to success: Those companies that can manage this well will likely be the ones to survive in the long term.
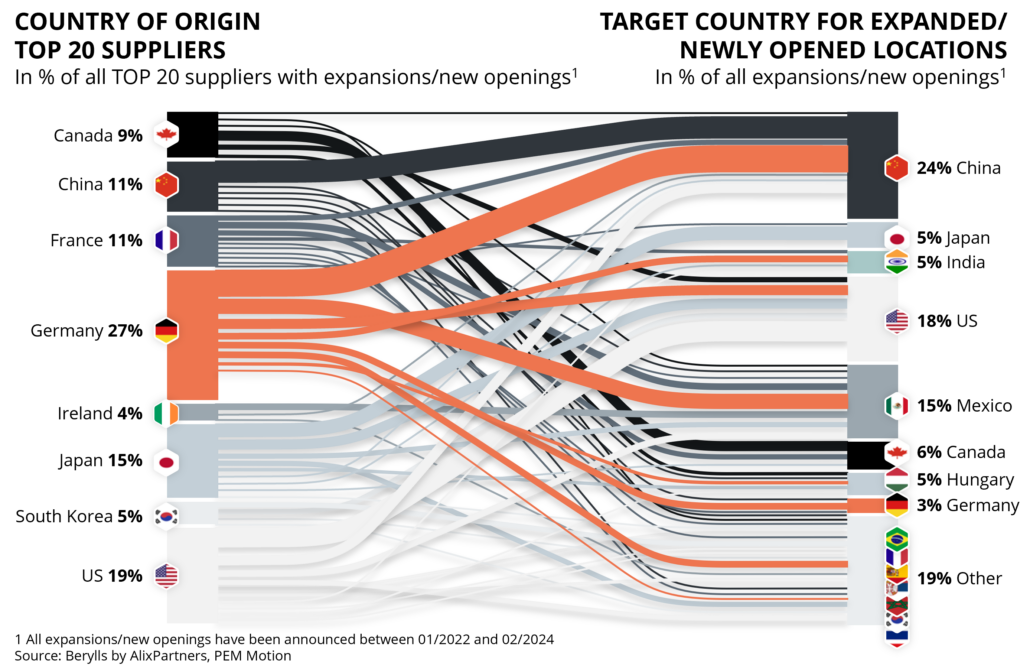
Battery-News: What would you recommend to automakers to accelerate the development of high-performance and cost-efficient batteries?
Timmer: Strategic partnerships – even though thatʼs not a new concept. In an environment that remains fluid, with no established technological standard, it is essential to forge new collaborations and reassess existing ones. Only this way can technological and financial risks be managed effectively. This importance is evident in examples like the Automotive Cells Company, a joint venture by Renault, Saft, and Mercedes, or the long-standing partnership between Northvolt and BMW, which was recently terminated. These collaborations hinge on trust and development roadmaps. What matters most is how innovations can be integrated into vehicles and determining the right time to bring these advancements to market. OEMs can only keep their market promises if they have a clear understanding of their suppliersʼ strategies and plans – particularly in the cell and battery sectors. On the other hand, suppliers need transparent information on production volumes, quantities, technology platforms, and timelines. This level of collaboration requires genuine partnerships, as it cannot be achieved in a traditional supplier-customer relationship.
“When tens or even hundreds of thousands of batteries begin to return, we will need a well thought-out logistics concept which doesn’t yet exist.”
Battery-News: Recycling volumes are expected to grow significantly by 2030. What challenges will this bring for companies?
Timmer: There are several fundamental, unresolved questions – particularly how the flow of spent batteries will be managed and how the logistics network behind it should be organized. When tens or even hundreds of thousands of batteries begin to return, we will need a well thought-out logistics concept which doesn’t yet exist. This involves standard situations as well as exceptions. In the recycling process, I see the central challenge less in the technology – whether hydrometallurgical or pyrometallurgical processes are used – but more in the logistics, transport, and material flows that enable this process in the first place.
Battery-News: Can you elaborate on this?
Timmer: Imagine a defect battery needs to be returned – whether due to an accident or other damage. Even an intact battery is classified as hazardous material. A damaged one poses an even greater risk. How exactly will it be transported? How can such batteries be safely recycled? These questions relate to logistics and the necessary standards for handling them. In Germany, we’re also seeing a delayed ramp-up of electric mobility, exacerbating the issue and resembling a chicken-and-egg problem. What comes first? The electric vehicle or the charging station? I recognize a similar scenario with recycling: Should we first build sufficient recycling capacity or prioritize logistics for battery returns? Recycling capacities exist, but theyʼre underutilized due to a lack of logistics and standards. Addressing this missing link is crucial for establishing a circular economy for batteries.
Battery-News: Is the circular economy already a focus in consultancy, or is it overshadowed by more pressing issues?
Timmer: For cell manufacturers, questions like “What will I do with a vehicleʼs battery in five years?” are not a priority right now. Their concerns are elsewhere – quality control, supplier management, securing cathode materials, or simply getting factories built. Securing necessary permits in countries like Hungary, Germany, or France, environmental concerns, and workforce recruitment are currently at the forefront.
“A circular economy is not at the top of the agenda. Currently, we are dominated by operational challenges that we need to solve in order to be able to bring electric mobility to series production on a large scale.”
Battery-News: In Germany, however, thereʼs increasing talk about a circular economy.
Timmer: Thatʼs true, but itʼs not at the top of the agenda. Right now, operational challenges dominate as we work to scale electric mobility. There are clear EU-level requirements for how much recycled material must be in batteries by certain years, but implementation is extremely difficult. Many battery manufacturers struggle to meet these quotas. Also, todayʼs batteries often last much longer than initially anticipated. Yes, there is production waste and batteries from accident vehicles, but this is far from enough to meet EU requirements. Building a stable supply chain is also challenging. Adding to this are import tariffs, local content conditions, and export restrictions, raising questions about whether cell manufacturers will even be able to export batteries to the United States in the future. This makes the problem even more complex. Still, a circular economy remains an important issue.
Battery-News: …with very ambitious targets.
Timmer: Yes, indeed. By 2030, 70 percent of batteries are expected to contain recycled materials. The remaining 30 percent could be split into 20 percent second-life use and ten percent reconditioning. But there are significant obstacles. Take second-life batteries, for example: Stationary energy storage has completely different requirements than vehicle batteries do. What homeowner installing a photovoltaic system would want to put a spent vehicle battery with 80 percent residual capacity and some risk in their basement? Even with overcapacity, battery manufacturers are naturally more interested in selling new products and maximizing factory utilization than prioritizing recycling – despite European legislative requirements.
Battery-News: How do you assess current developments in solid-state batteries or other innovative technologies?
Timmer: There are already numerous partnerships in the field of solid-state batteries. Investments by Volkswagen and BMW Group in companies such as Solid Power or QuantumScape are just two examples. However, these collaborations often face a similar challenge, being two worlds colliding with each other. On the one hand, the highly standardized, process-driven approach perfected by automakers over decades, and on the other, the dynamic, fast-paced innovation culture of start-ups and tech players. The practical demands large automakers place on these partnerships often aren’t met – at least not in the way these companies expect it or are accustomed to.
“Currently, the focus is more on maximizing existing factory utilization and achieving short-term success rather than allocating resources to disruptive innovations.”
Battery-News: How would you summarize the status quo of Europeʼs battery industry?
Timmer: Cell manufacturers are about to face a dilemma: On the one hand, they must build capacity to meet legal requirements, such as localized production in Europe. On the other, we already see overcapacity, forcing them to take significant risks with their investments. Currently, the focus is more on maximizing existing factory utilization and achieving short-term success rather than allocating resources to disruptive innovations such as solid-state batteries. Ramp-up stability hasn’t developed as expected in recent years. The pressure to drive both growth and localization simultaneously is hindering resource allocation for disruptive developments.