Precise and fast production processes are crucial in mass production of battery cells. Even small time or energy savings in production steps add up to significant increases in output, positive cost effects, and reduced carbon emissions. Product transportation is said to be a key aspect for increasing efficiency in battery production.
Transport route with continuous material flow
In this area, Beckhoff Automation from Verl, Germany, offers new possibilities with its intelligent linear XTS transport system and powerful PC-based control technology. With traditional linear transport systems, material flow is often interrupted by return paths with empty runs. In contrast, XTS allows a circulating route that enables continuous material flow and increases the entire production line’s efficiency. According to Beckhoff, the active XTS travel path is equipped with individually controllable “movers” that can brake, accelerate, position, or exert a constant force along the entire route, whether stationary or in motion. This enables gentle and safe handling of the products to be transported as well as flexible changes between different formats and leads to significantly reduced buffer times.
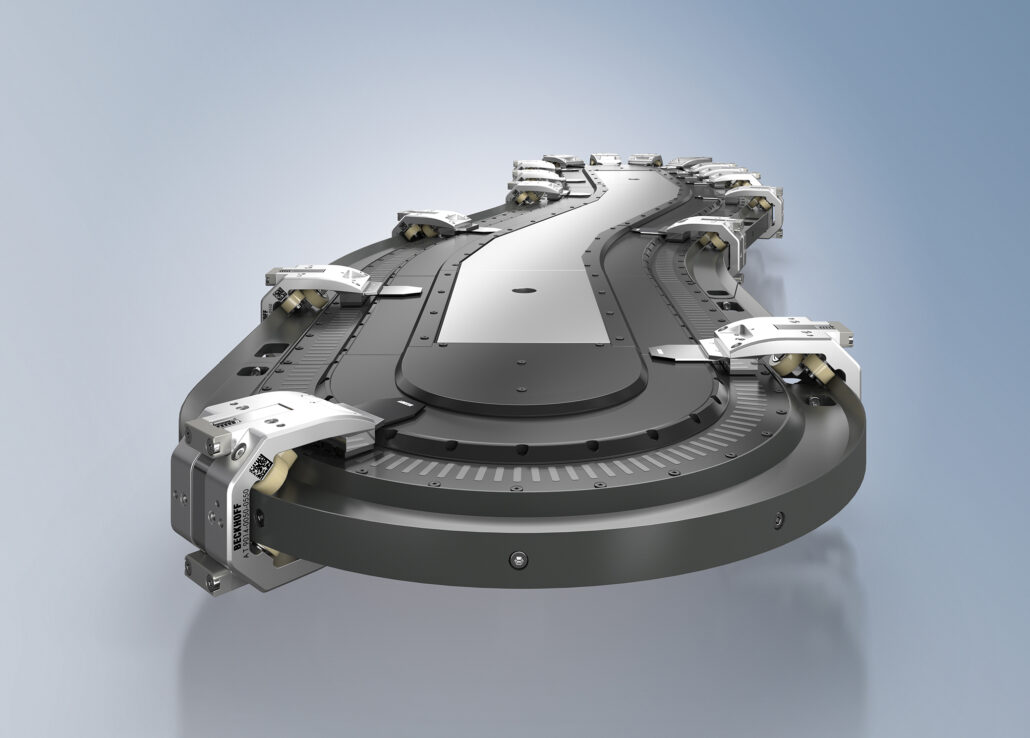
Modular system for flexible product transportation
XTS is primarily characterized by its modularity. The length of a system can be finely scaled with variable modules, which enables a precisely fitting and expandable system size. For this purpose, both straight motor modules of different lengths and curved modules with different bending radii are available. There are also modules with an extended range of functions – for example, for contactless energy and data transfer to the movers via “No Cable Technology” (NCT) – as well as modules with a reduced range of functions for sections without process stations (“EcoLine motor modules”). Beckhoff claims this is fully compatible and makes it possible to optimally adapt the transport route to the specific processes of battery production and make the best possible use of the available space.
Optimum synchronization
According to Beckhoff, the movers as well as other processes can be controlled in parallel and synchronized to a high degree using the company’s PC-based control technology and the industrial Ethernet communication system “EtherCAT”. This in turn leads to quality improvements or material savings in the process. In addition, stops for process steps such as loading and unloading are to be avoided, thus eliminating downtimes. Movers running on two different systems can also be linked to each other via software. According to Beckhoff, this increases payloads or reduces product distances. XTS enables transport speeds of up to four meters per second with accelerations of up to 10g, which ensures a high product output. The speed can be individually adjusted to meet the requirements of the respective production steps. The highly flexible product transportation is said to offer numerous advantages throughout the entire manufacturing process.
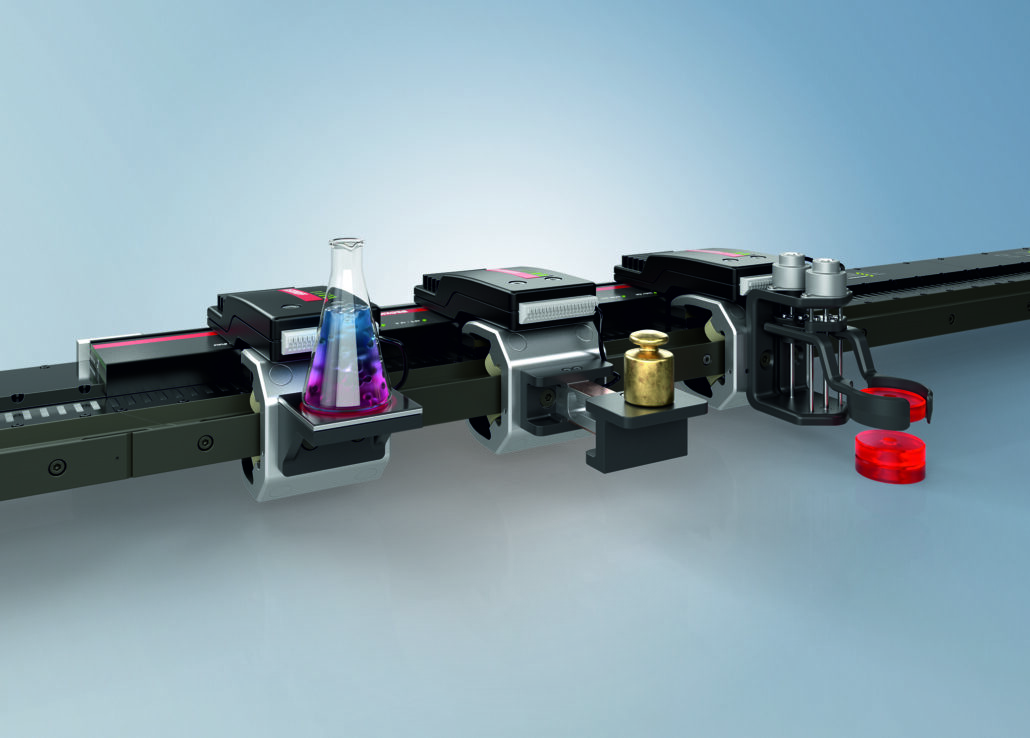
Advantages in cell assembly
In cell assembly, where the battery cells’ individual parts are joined together, XTS is said to offer considerable advantages thanks to its flexible scalability and the option of individual product transportation. According to Beckhoff, the ability to clamp cell components safely and gently as well as the option to switch flexibly between different product formats ensure high precision and efficiency during this specific process.
Advantages in optical inspection
For the optical inspection of battery cells, the movers’ or the cells’ positions can be synchronized with a camera. It is also possible to use several cameras at once for a more versatile cell inspection, which saves time, reduces the number of stations, and improves quality by increasing accuracy and the clear reference of the images.
Advantages during cleaning
Cleaning the battery cells – whether by plasma or chemical processes – can be carried out efficiently by rotating the product mechanically or electrically on the mover. For product rotation, an actuator can be supplied and controlled with the help of contactless energy and data transfer (NCT). Both options are designed to ensure thorough cleaning and preparation of the cells for the next production steps.
Advantages in adhesive application
The adhesive can be applied to the cell on the fly, using either liquid adhesive or tape. This avoids process stops, accelerates the bonding process, and ensures that the adhesive is applied evenly, quickly, and precisely.
Advantages in the joining process
As XTS enables the simultaneous joining of several battery cells, this results in high precision and speed in the joining process and therefore an increase in the efficiency of the entire production line. In addition, the number of cells to be joined can be flexibly adjusted using software.
Advantages in reject detection
According to Beckhoff, XTS makes it possible to efficiently discharge tested battery cells that have been declared as bad parts at an early stage. Thanks to end-to-end tracking and differentiated control of the movers, the system can assign good and bad parts to different processes. This ensures fast and precise separation of the cells, improves the quality of the final product, and prevents unnecessary further processing of bad parts – ultimately saving disposal costs.