This is common sense: The automotive industry has to transform itself. Therefore, Europe must ensure that it has its own expertise and capacities, particularly in the area of battery cell production. With the support of policymakers, significant investments are currently being made in developing battery cell production. But how can European companies position themselves in line with the market?
More than 135 billion dollars by 2027
Market researchers at Markets and Markets expect global demand for lithium batteries for electric vehicles to increase by 19 percent annually over the next five years. Accordingly, sales are expected to grow from 56.4 billion US dollars in 2022 to 134.6 billion dollars by 2027 with a capacity focus of 50 to 110 kilowatt-hours.
CATL is undisputed world market leader
The leading suppliers come from China, South Korea, and Japan. CATL covered more than a third of the global market for electric vehicle batteries in the first half of 2023, while BYD moved into second place with just under 16%, ahead of LG Energy Solution with 14.5%. Battery heavy-weights such as Panasonic, SK On, CALB, and Samsung SDI follow with single-digit percentages. The top-five manufacturers alone cover more than three-quarters of the global market. It is common for their production facilities to be built as turnkey solutions by large project developers.
Flexible design of production facilities
One relevant aspect is the rapid pace of development in battery cell technology. Today, lithium-ion batteries in the form of pouch cells, round cells or prismatic cells are common, but new formats, dimensions, or materials could soon become relevant – such as All-/Almost-Solid-State Batteries (ASSB). Facilities have to be flexibly adaptable to make a production system fit for the future. Therefore, state-of-the-art digitalization is essential – for example in the form of digital twins. A digital image of the system makes it easier to adapt production, as the impact of a new product on the system can be tested virtually in the early planning phase, and the physical implementation only takes place once all problems have been solved in the simulation. This can also be used later during commissioning, maintenance, and servicing. However, this also requires appropriate digital transformation skills. Start-ups in particular often need support here.
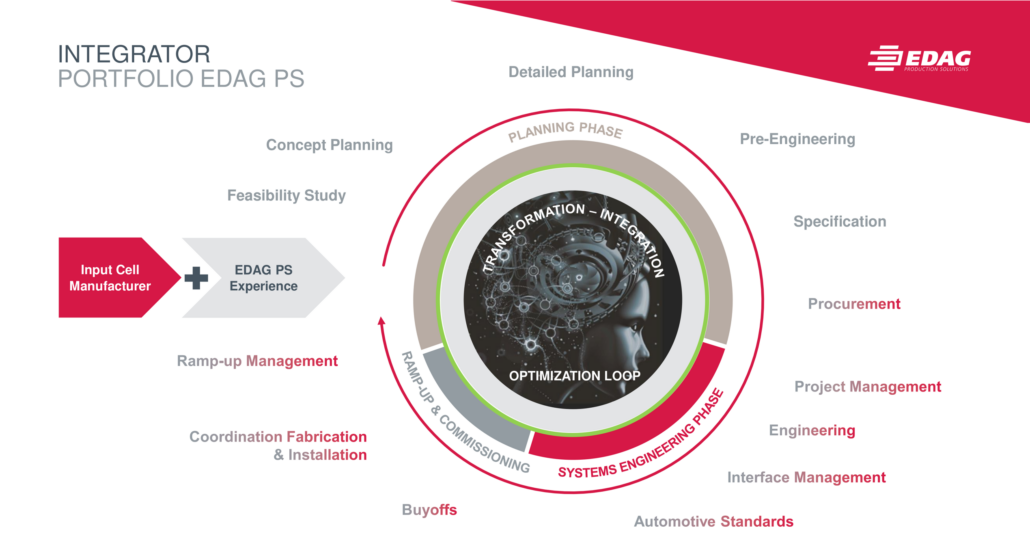
Another point is sustainability in production. Many electric vehicle batteries will soon be available for re-use and recycling. The EU has already issued regulations on the utilization rate of recycled materials and the carbon footprint of production. These – and other, possibly stricter regulations that may follow – must be considered when setting up a new production facility. Also, operating costs determine the competitiveness of European manufacturing solutions compared to those of Asian suppliers with lower investments. Better OpEx values – for example, due to a significantly lower reject rate or higher throughput – can reduce total cost of ownership (TCO) despite higher raw material and energy costs in Europe.
Do turnkey providers have an advantage?
So-called turnkey providers can rely on extensive experience. As project developers, they offer all the necessary expertise under one roof, so little coordination effort is required. They utilize proven technology and offer to build clones of comparable Asian production facilities in Europe – in a comparatively short period of time. There are no suppliers of comparable size in Europe who could offer everything from a single source. At best, an integrator approach offers alternatives. Various competencies are required for the physical construction and launch of industrial production, including project development, industry-specific features, and elements of process engineering. These must be brought together in an appropriate consortium. The essential steps of such a project include:
- setting up a central project management team to coordinate the consortium participants and the various tasks;
- a feasibility study as well as concept planning, detailed planning, and specification of the equipment through to the translation into corresponding tenders;
- construction of the systems;
- supervision of equipment installation in the production hall;
- commissioning;
- system ramp-up with troubleshooting and optimization measures.
Linking these together takes time and effort, as these are usually highly customized solutions, which can harm competitiveness: The investment costs (CapEx) will be higher than with a turnkey solution. At least from this point of view, Asian providers hold an advantage.
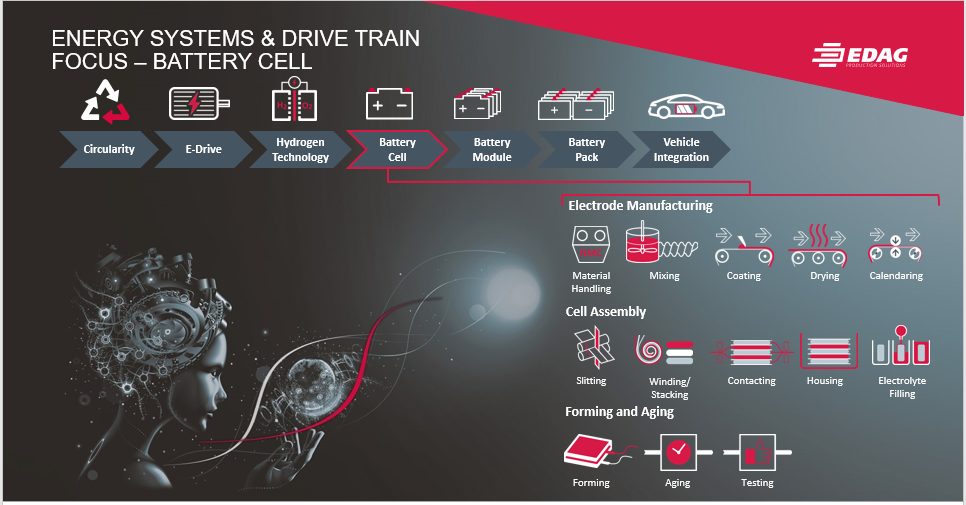
Total costs are a decisive factor
In fact, turnkey solutions repeatedly show weaknesses that hinder efficient operation. Problems with throughput and high reject rates cause difficulties for operators. Issues such as CE labeling and other European standards – for example, occupational health and safety – also pose an enormous challenge for project developers from outside the EU. These cannot always be resolved satisfactorily for the client. They then have to carry out time-consuming rework, which erodes the time advantage and drives up initial investment.
European collaborations
A merger of European specialists – whether as a consortium, a joint venture, or a similar construct – therefore offers opportunities to survive in the seemingly hopeless competition with the industryʼs giants with the help of economically attractive solutions. In order to remain competitive in this area, the European industry needs systems that are powerful and highly efficient, produce modern cells, and can be flexibly adapted to the dynamic technical developments. Many suitable suppliers have specialized knowledge and sustainable solutions in their respective fields. The Battery Atlas, for example, provides an overview of relevant manufacturers at all stages of the value chain.
Production engineering, simulation, and more
The question is, who can coordinate and manage such a merger? On the one hand, general production skills are required here, but also specific expertise in the special features of battery production. EDAG Production Solutions can take on this task and also become active in various areas. The company, for example, offers 360-degree production engineering – including plant planning and optimization – as well as process digitalization, and experience in simulation and virtual commissioning. Furthermore, the EDAG Group is involved in various committees and consortia for battery cell production, such as FestBatt and ProZell, so it can also draw on domain knowledge in this area. This is complemented by extensive industry contacts with companies at all levels of the value chain.