In order to ensure the highest levels of safety, reliability and environmental protection, leak testing is of great importance to the automotive sector in the production of fuel cell electric vehicles (FCEVs). Pfeiffer Vacuum has been helping automakers develop hydrogen-powered vehicles since the early days of this technology and is a key partner in providing leak detection solutions.
Safety, reliability and the environment
Leak testing is particularly important for the FCEV market to ensure that strict safety and operational standards are met. For example, it is mandatory that the fuel tank, which stores hydrogen, and the fuel cell stack, which converts hydrogen and oxygen into electricity through cold combustion, are tested for leaks. But it is not just the tank and stack that are tested several times during the production of an FCEV. This applies both to the components in the hydrogen circuit that carry the operating and cooling media and to the battery components that are also present in all FCEVs.
Finding the right leak detection method
Hydrogen fuel cell stacks, as the heart of an FCEV, present particular challenges for leak testing. The length of all the seals in a 120 kW fuel cell stack can be up to 1 km and must be fully tested. This process is further complicated by the fact that the dimensions of functionally relevant leaks are no longer visible to the human eye. A simple visual inspection is no longer sufficient. Repair is only possible once existing leaks have been located.
Due to the risks associated with the use of hydrogen as a flammable or explosive medium, leak detection is considered a safety-relevant aspect of the fuel cell manufacturing process. A variety of leak detection methods and test equipment are currently used in the industry. Standards in the field of leak testing, such as DIN EN 1779 or DIN EN ISO 20485, provide assistance in the selection of methods by identifying different leak testing methods and providing procedural instructions. Methods range from leak testing with air (pressure change and flow methods) to tracer gas methods using hydrogen, helium or mixtures of the two gases to be selectively detected.
“The great merit of DIN EN 1779, first published in 1999, is the systematic classification of the most important leak test methods used in industry and the decision support based on three clear criteria” explains Dr. Rudolf Konwitschny, leak detection expert at Pfeiffer Vacuum. These criteria are:
1. In which direction does the gas normally flow when it escapes from a leak? Out of the object or into the object?
2. Do I test only components of a test object or the test object as a whole?
3. Do I test integrally or localizing? Integral testing provides information on whether or not leaks are present. Localizing methods can determine where the leak is located.
After applying these questions, the standard leaves seven quantitative integral leak test methods based on air or tracer gases that are potentially suitable for testing a pressurized component.
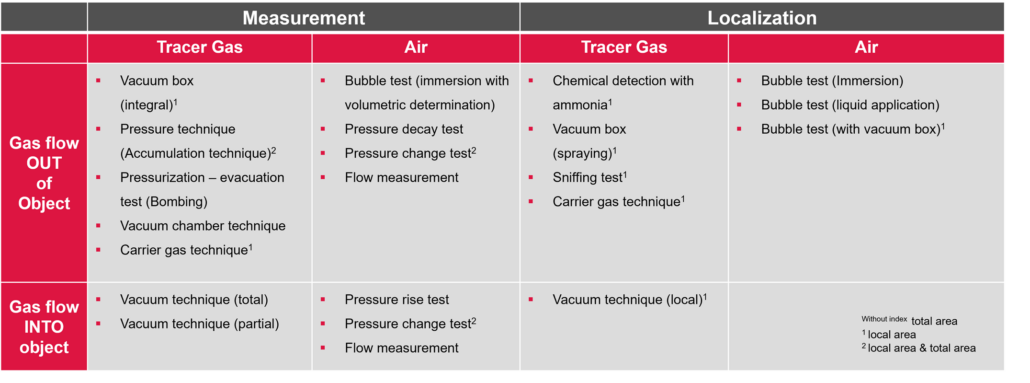
Figure 1: Selection criteria of the leak test methods according to DIN EN 1779
According to this pre-selection, both air and tracer gas methods can be considered for integral leak testing. This decision is influenced by a number of factors. The use of air for leak testing has the advantage of requiring little equipment, air is cheap and readily available compared to tracer gases, and inexpensive test equipment can be used. Disadvantages are limited minimum detectable leakage rate (standard leak rates down to a minimum of 1E-4 mbarl/s) and influencing factors such as temperature and volume. The strengths of air leak testing lie primarily in applications under isothermal conditions and in small volumes.
“A number of leak tests can be performed, for example, using the differential pressure method (which measures how much air is lost from the unit under test compared to a reference volume) or flow methods,” says Konwitschny.
ISO 22734, which describes leak testing of electrolyzers among other things, states that the cell stacks must be subjected to a common pressure test in which the oxygen and hydrogen sides of the individual stacks are connected to a common pressure source and tested simultaneously. Test conditions are also specified in the standard: The pressure should not be less than the maximum operating pressure and the test duration should be at least two minutes. Exact temperature conditions are also specified, but there is no explanation of the influence of these parameters on the test result. According to Konwitschny, this is an important aspect for manufacturers to consider.
Basically, air-based leak testing methods have physical limitations. Temperature is one of the most important environmental parameters. Depending on the size and volume of the part being tested, it can have a significant effect on the measured value of a pressure transducer. Konwitschny explains: “For parts such as the bipolar plate of a fuel cell, we are talking about temperature constancy in the range of 0.1 °C or even less. This is one of the reasons why, in comparative measurements in our application laboratory, we have found a wider spread of measured values with Micro-Flow methods than with test gas methods. In our experience, the instrumentation and process capability of test gas methods are superior. The test gas helium or mixtures containing helium give even better results than hydrogen due to the lower and more constant background signal.
The impossibility of perfect control of the test environment, together with the requirement for detection limits below 1E-4 mbarl/s, makes the use of test gases mandatory in many applications. Tracer gases such as helium are more expensive than air, but have the advantage of allowing lower detection limits and often shorter cycle times. The decision between air and tracer gas should therefore be made in the context of the prevailing conditions and the leak test requirements.
Another important factor in choosing a leak testing method is the investment and running costs. “If you are starting your production with low volumes, the initial cost of the test system is important because you have to allocate it to the part you are going to produce. For high-volume production, the cost of a test system is negligible. Instead, the focus is on speed and operating costs: you need ultra-short cycle times,” advises Konwitschny.
In addition, there is the question of what to do with components that exceed the specified PASS/FAIL criterion during integral testing. While the loss of a single bipolar plate may be tolerated due to volume production requirements, a stack is definitely a component where leak localization and rework are worthwhile. For leak location, only tracer gas methods are practical. Selective detection in air is only possible with specific tracer gases such as helium. In the hydrogen economy, helium is superior to hydrogen-containing gas mixtures because of its chemical and electrical inertness, selectivity and detection limit.
FCEV Leak Detection Systems from Pfeiffer Vacuum
Pfeiffer Vacuum is the only company in the world that manufactures equipment for both air and tracer gas leak detection. This broad product portfolio enables the company to provide customers with objective, application-specific advice on the proper methodology for leak testing FCEV components. With many years of experience and involvement in key developments in hydrogen powered mobility, the company can analyze a customer’s requirements and bring them into line with current regulations.
The company advises on:
– Selecting the leak detection solution for specific application(s)/budget(s)
– Determine the optimal procedures, test criteria and equipment list
– Identify potential locations where leaks may recur
– the design of test procedures to objectively measure a specified limit, and
the subsequent localization of leaks, if necessary
– the feasibility studies for leak detection, if required
Feasibility studies, which require a high level of understanding of the technical requirements of a product or system, are used to determine the most appropriate leak detection method. This can be particularly useful when new products are about to be launched or when the cycle times for leak testing existing products need to be optimized. Pfeiffer Vacuum’s application teams offer feasibility studies both during the development of FCEV systems and during the manufacture of the final product. This also includes customized solutions to save costs and increase the efficiency of leak testing.
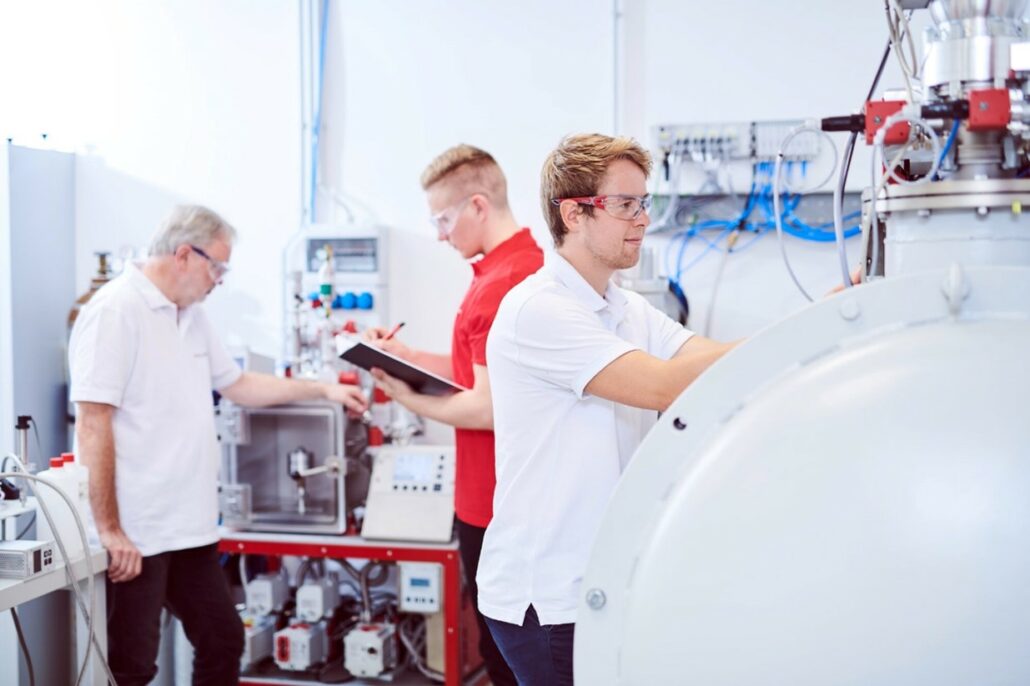
Figure 2: In the in-house application laboratory, Pfeiffer Vacuum application experts assist in developing a suitable leak test method