In battery cell production, the requirements for quality assurance and optical defect detection have increased enormously. To meet these challenges, Dr. Schenk GmbH has significantly improved its camera-based AI systems. In its most recent interview, Battery-News talks to Jochen Sander, responsible for global battery product management, about the specific requirements of the industry, the innovations in AI technologies, and the advantages of modular, real-time capable AI in battery cell production.
Battery-News: How have current requirements for optical defect detection in electrode production prompted Dr. Schenk to expand its AI systems in such a significant manner?
Jochen Sander: From electrode coating to stacking and winding, AI faces a variety of challenges. Often the smallest, low-contrast defects need to be found on a clearly structured background [see Fig. 1; editorʼs note]. Our customers require precise classification at high speed, which means reliable differentiation between various defects. We currently have requests for classification rates of up to 99.99%. At the same time, however, the systems have to be very easy to teach and extremely robust in the face of the variability of processes and materials. In order to meet these and other contradictory requirements, we have significantly enhanced our AI technologies.
Battery-News: How did you proceed in order to better implement these demanding requirements?
Sander: We pursued two central approaches. First, we made our AI even more modular. This means that it consists of various specialized modules, each of which is optimized for a specific task. The modules can be combined as required. Second, we integrated the AI evaluation directly into the camera hardware. Each Dr. Schenk camera has extremely high computing power, which enables extremely fast and efficient AI processing in real time.
Battery-News: Other providers are also pursuing a modular AI approach. What is special about the Dr. Schenk solution?
Sander: The sophisticated, close interaction of the modules and their flexibility. Most of our customers start with a simple combination of classic feature recognition and a decision tree. The feature recognition determines geometric properties such as defect size, shape, et cetera, and the decision tree uses these to create a precise and comprehensible distinction between the different defects. This means that our customers have a reliable initial classification after just one day or two days, which they can easily expand themselves. Only a few defect images are required, which is very helpful during ramp-up.
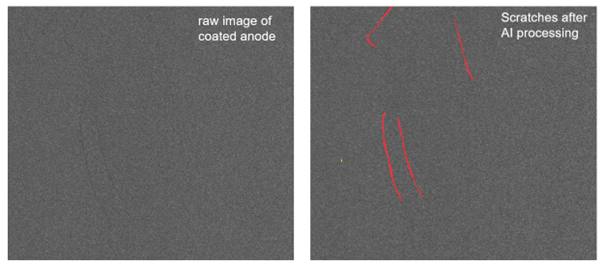
If requirements change or increase, additional modules can be used at any time. The existing AI can continue to be used, and a new detection method can only be added for selected defects, for example. This keeps the AI clear and efficient. Once images have been annotated, they can be used in all AI modules. This makes extensions really simple and practical for use, even without AI experts [see Fig. 2; editorʼs note].
Battery-News: You spoke earlier about real-time AI. What do you mean by that?
Sander: Real-time is a very flexible term. We understand it to mean that the camera evaluation is significantly faster than the usual process steps in electrode production. The speed can be illustrated by an example from the paper industry: Here, we inspect twelve-meter-wide paper webs at speeds of up to 2,000 meters per minute. Our AI in the cameras processes a total data rate of approximately 360 gigabit per second. That is over one million times more than an HD TV stream.
Battery-News: That sounds impressive. How do you achieve that?
Sander: Our self-developed cameras can record more than 280,000 scans per second, and in them we use FPGAs, so-called Field Programmable Gate Arrays. These logic ICs are configured specifically for a task and carry out the evaluation in the hardware. This makes them much faster than graphics processors.
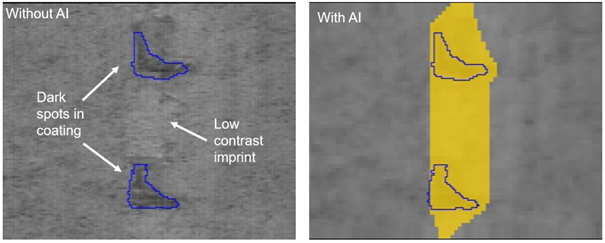
Battery-News: And how do battery manufacturers benefit from this performance?
Sander: Primarily due to the fact that more complex evaluations or pre-processing can be carried out in the cameras, which leads to better results. But the reliability of the entire system also increases significantly, as only a single PC is required. This machine only evaluates select, small image sections of the defects and is primarily used for data storage and as a system interface. Experience has shown that PCs are one of the weakest components in the system. We offer a ten-year warranty on our cameras.
Battery-News: What do you consider to be the most important aspect of AI-supported inspection in general?
Sander: Despite all the impressive possibilities of modern AI processes, there is one simple truth: Powerful AI requires high-quality images. We have found that better recognition is achieved faster with multiple illuminations from different directions. AI is the icing on the cake that can extract even more information from the image data. That is why we use our own multi-channel lighting, the MIDA technology, and customize the required optical configuration consisting of lighting and cameras. Another point is protecting the customer from the complexity of AI. The great art of our development is hiding this complexity behind an easy-to-use interface.