There are numerous new developments in the battery market. This also applies to the application area of vacuum technology. Battery-News spoke to Dr. Philipp Schurig, Market Manager at Pfeiffer Vacuum and responsible for industrial leak detection, about requirements, challenges, and trends in this field of battery production.
Battery-News: How has battery manufacturing developed in recent years with regard to your company?
Dr. Philipp Schurig: A lot has happened in this market since our last interview in December 2020. The number of planned gigafactories in Europe has continued to rise. The established cell manufacturers and system suppliers from Asia play a major role here, as they have many years of experience in the realization of such large-scale projects. At the same time, battery recycling is also becoming increasingly important. In view of the increasing demand for battery cells, high demands are being placed on the productivity of gigafactories – but also on fast service in the event of failures or downtime. The high quality of European plant and mechanical engineering companies and their regional supply chains and service networks is a major advantage over the Asian players. In any case, the increasing European and Asian activities of plant manufacturers in the battery market have triggered a growing demand for vacuum technology, which we can meet with our product portfolio.
Battery-News: What are the current drivers in the market? What trends and associated challenges do you currently recognize?
Schurig: There are various driving forces in this dynamic market, both in terms of battery chemistries and production technology. New chemistry variants – such as lithium iron phosphate batteries, sodium, or sulphur compounds – and new types such as semi-solid-state or all-solid-state based on polymers are constantly being established. These new chemistries pose their own questions – for example, which production technologies are used for them and whether existing production lines can be used. In addition, the battery chemistries and types are at different stages of development, from research to prototypes. From the perspective of plant engineering, the carbon footprint of battery production as a whole must be significantly reduced in order to achieve the politically agreed targets. The biggest levers for this are the use of significantly more energy-efficient products as well as innovative processes that can completely replace energy-intensive production steps.
There is consensus that European plant engineering must find innovative solutions for existing processes in order to reduce the gap to the dominant Asian market.
Dr. Philipp Schurig,
Pfeiffer Vacuum
Battery-News: What insights did you gain as a participant in the Future Battery Forum in Berlin last year?
Schurig: We have noticed that there is a consensus that European plant engineering must find innovative solutions for existing processes in order to reduce the gap to the dominant Asian market. The innovative strength, knowledge of European regulations, and decades of experience from the conventional automotive industry will be essential for European manufacturers. Companies and universities are already working together on innovative technologies that can be used to improve established processes, such as laser drying, or even replace them completely, which is the case with dry coating. Currently, more and more consortia of companies are forming that offer their expertise in the realization of turnkey solutions and partial solutions for battery production.
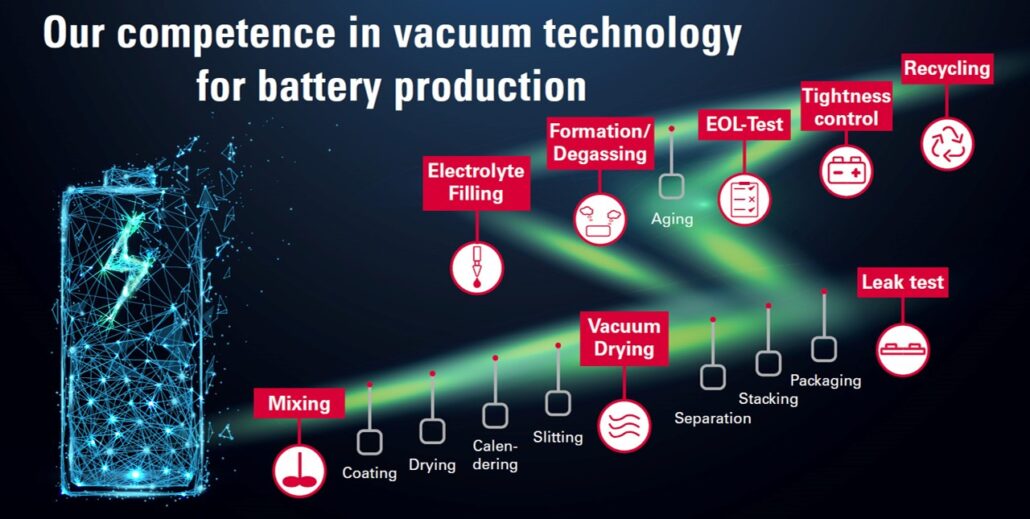
Battery-News: While Europe is increasingly developing into a market for cell production, the recycling market is also growing. Where and with which solutions has Pfeiffer Vacuum positioned itself in the battery cell lifecycle?
Schurig: We are active with our products in quite some phases of this lifecycle. Our diagram only shows the steps within a battery gigafactory in which vacuum is required. However, vacuum or leak testing technologies are already used in the manufacture of materials for production, for example in the coating of the initial coils for the coating process step or in the upstream leak testing of the cylindrical and prismatic battery cell components.
Battery-News: What particular innovations do you like to look back on?
Schurig: One of our latest product innovations is the Okta ATEX series of roots pumps with a pumping speed of 5,400 or 8,100 cubic meters per hour. Thanks to their design and temperature monitoring, these pumps provide a high level of explosion safety. The high pumping speed, which is particularly required for vacuum drying and recycling, also enables a more efficient production process. Another interesting parameter can be the composition of the extracted gas. Our GSD 350 mass spectrometer – especially as the ThermoStar version – makes it possible to analyze the gas up to a resolution of 300 u by extracting very small quantities of gas of just one cubic centimeter. In addition to these new products, we can also offer individual services for the battery market, such as our leak detection. This enables customers to find the right solution for their leak testing challenges together with our application specialists at an early stage and without having to make their own CAPEX investment.
Leak testing of batteries is an important quality feature for the battery market, as their safety and service life are of paramount importance for both manufacturers and users.
Dr. Philipp Schurig,
Pfeiffer Vacuum
Battery-News: What exactly can a prospective customer expect from these services? What does the service offer customers especially from the battery market?
Schurig: Our leak detection services include feasibility and cycle time studies, contract measurements and residual gas analyses. Leak testing of batteries is an important quality feature for the battery market, as their safety and service life are of paramount importance for both manufacturers and users. The biggest challenge for new technologies is usually the determination of a ‘functional’ leak tightness requirement or the most suitable leak test method. A feasibility study can be useful for both problems. We recently showed how such an analysis can be carried out in a webinar. For leak detection, we maintain application laboratories in the USA, in Germany, and in China, which are equipped with state-of-the-art vacuum, measurement and analysis technology and cover the 15 test methods in accordance with DIN EN 1779/ISO 20485. The measurement and analysis technology is designed for all common industrial technologies, such as leak testing with air or with tracer gases and for quadrupole mass spectrometry.
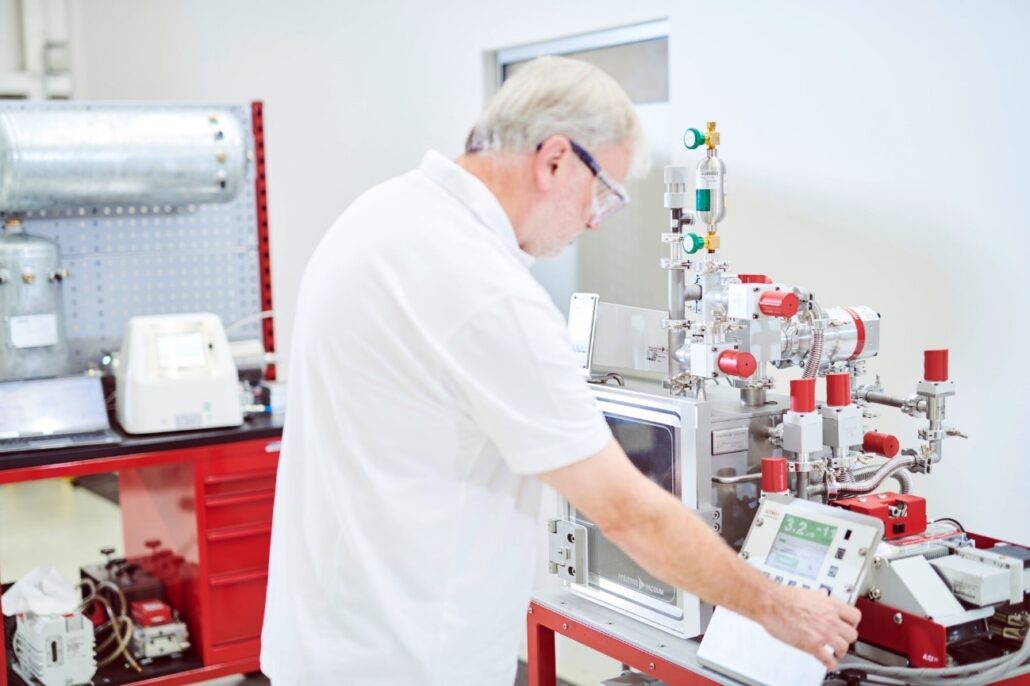
Battery-News: Why is the tightness of batteries so important? How exactly can it be checked in cell production and what are the challenges involved?
Schurig: The safety and service life of batteries are ensured with the help of leak testing, from the cell to the battery cooling system to the battery pack. Looking at the battery cell alone, leak tightness can be checked at several points up to the finished product: starting at component level – for example, at the lid and body of the batteries –, directly before electrolyte filling or as an end-of-line test. A major challenge in the industrial leak testing of batteries is cycle time, which is extremely fast due to a gigafactory’s necessary efficiency. As a result, only random sample testing, testing of individual batteries from production batches, or the batch method in the form of simultaneous testing of several battery cells are usually conceivable. Despite the enormous effort involved and the associated costs, leak testing is essential from a safety perspective. Depending on the battery chemistry, the penetration of moisture into the batteries can lead to the formation of highly toxic gases or liquids or trigger other reactions in the battery that severely jeopardize the integrity of the battery.
Leak testing will also play an important role for solid-state batteries. Just because there will no longer be any liquid electrolyte does not mean that the other components within the battery cannot still react strongly with moisture.
Dr. Philipp Schurig,
Pfeiffer Vacuum
Battery-News: With solid-state batteries, there is no longer any electrolyte in the cells, and cooling may no longer be necessary in its current form. Will it still be necessary to test the cells for leaks or are you thinking about new developments in this area?
Schurig: Leak testing will also play an important role for solid-state batteries. Just because there will no longer be any liquid electrolyte does not mean that the other components within the battery cannot still react strongly with moisture. A well-known example of this is novel battery chemistries containing sulphur, which can form hydrogen sulphide on contact with moisture. As research in the field of solid-state batteries is still at an early stage, it is not yet possible to estimate exactly how leak testing will be carried out in industrial production. However, we can already provide support today – be it with vacuum pumps that comply with ATEX directives, with our portfolio of analysis equipment, or with our leak detection service that enables meaningful studies without having to make a long-term investment in equipment.